Hot Tapping Pipeline Services
Hot-tapping a pipeline is a specialized procedure used to create a new connection or branch on a live, pressurized pipeline without interrupting the flow of the substance inside, such as gas, oil, or water. The process involves attaching a fitting to the pipeline, then using a hot-tap machine to safely drill into the pipeline while it remains operational. This allows for modifications, maintenance, or extensions to be performed without costly or disruptive shutdowns. Hot-tapping is widely used in industries that rely on continuous pipeline operations and requires specialized skills and equipment to ensure safety and efficiency.
What You Need to Know About Hot Tapping Pipeline Services
Hot tapping, also known as pipeline hot tapping, is a specialized procedure used to create a branch connection on a live, pressurized pipeline without interrupting the flow of fluids or gases. This technique is crucial in industries such as oil, gas, water, and chemicals, where continuous operation is essential. By utilizing hot tapping pipeline services, operators can perform maintenance, and repairs, or add new connections to existing pipeline systems without costly or disruptive shutdowns. Here’s everything you need to know about hot tapping:
What is Hot Tapping?
Hot tapping is the process of connecting a new pipeline or making repairs to an existing pipeline that is still in operation. It involves cutting into a pressurized pipeline using specialized equipment, allowing for the installation of valves, fittings, or new branch lines. This procedure is performed while the pipeline is still in service, so there is no need to depressurize the system or halt the flow of product, which can save time and reduce costs.
How Hot Tapping Works
Preparation: Before performing a hot tap, the section of the pipeline where the tap will occur is thoroughly inspected to ensure it can handle the procedure. This includes evaluating the pipeline material, pressure, and the nature of the contents flowing through it.
Attaching the Fitting: A fitting, often a welded or mechanical saddle, is installed onto the pipeline at the desired location for the new connection. This fitting serves as the attachment point for the hot tapping machine.
Hot Tapping Machine Setup: The hot tapping machine is connected to the fitting. This machine contains a cutter and a sealing mechanism, allowing it to drill into the pipeline without releasing any of the pressurized contents.
Drilling: The machine cuts through the pipeline wall, creating an opening for the new branch or valve. During this process, the machine ensures that the internal pressure of the pipeline is maintained, preventing leaks or spills.
Completion: Once the drilling is complete, the cutter is withdrawn, and the new pipeline branch or valve is installed. The hot tapping machine is then removed, leaving the pipeline fully operational.
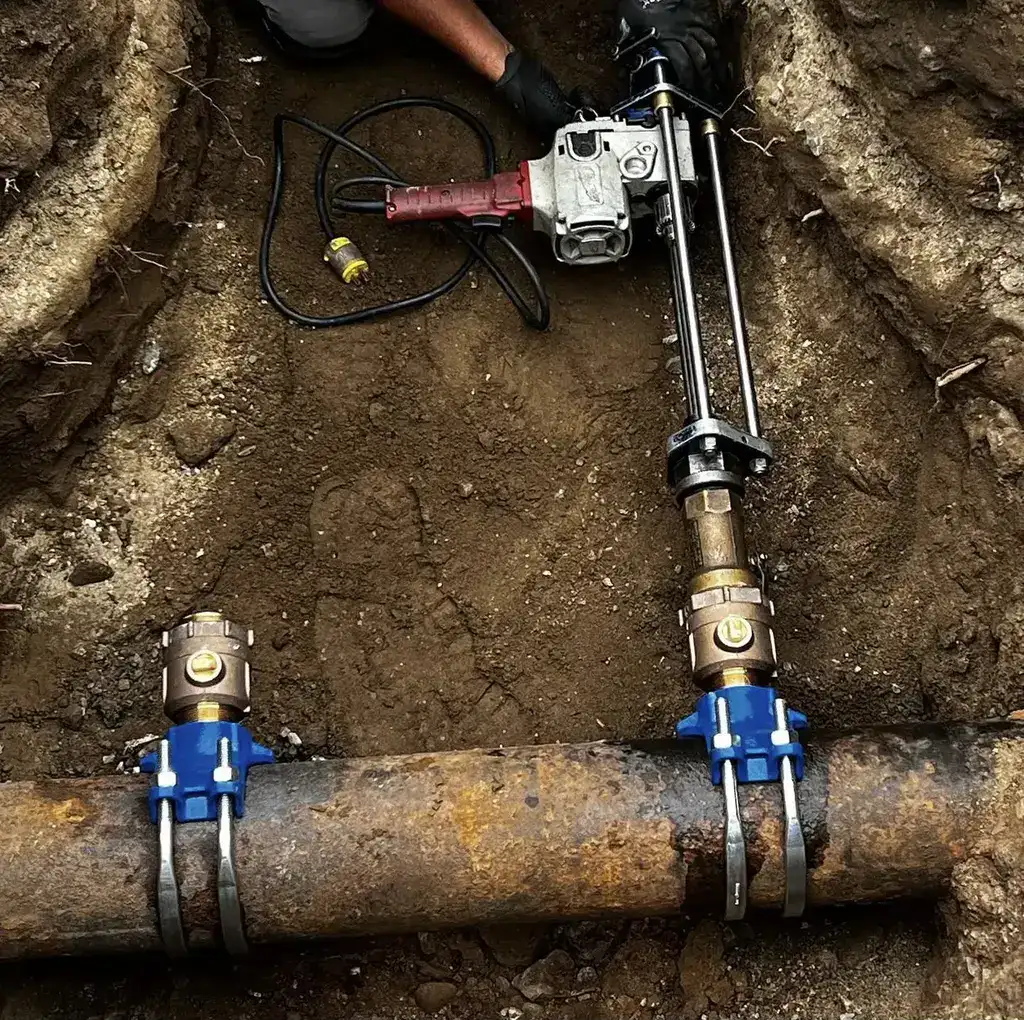
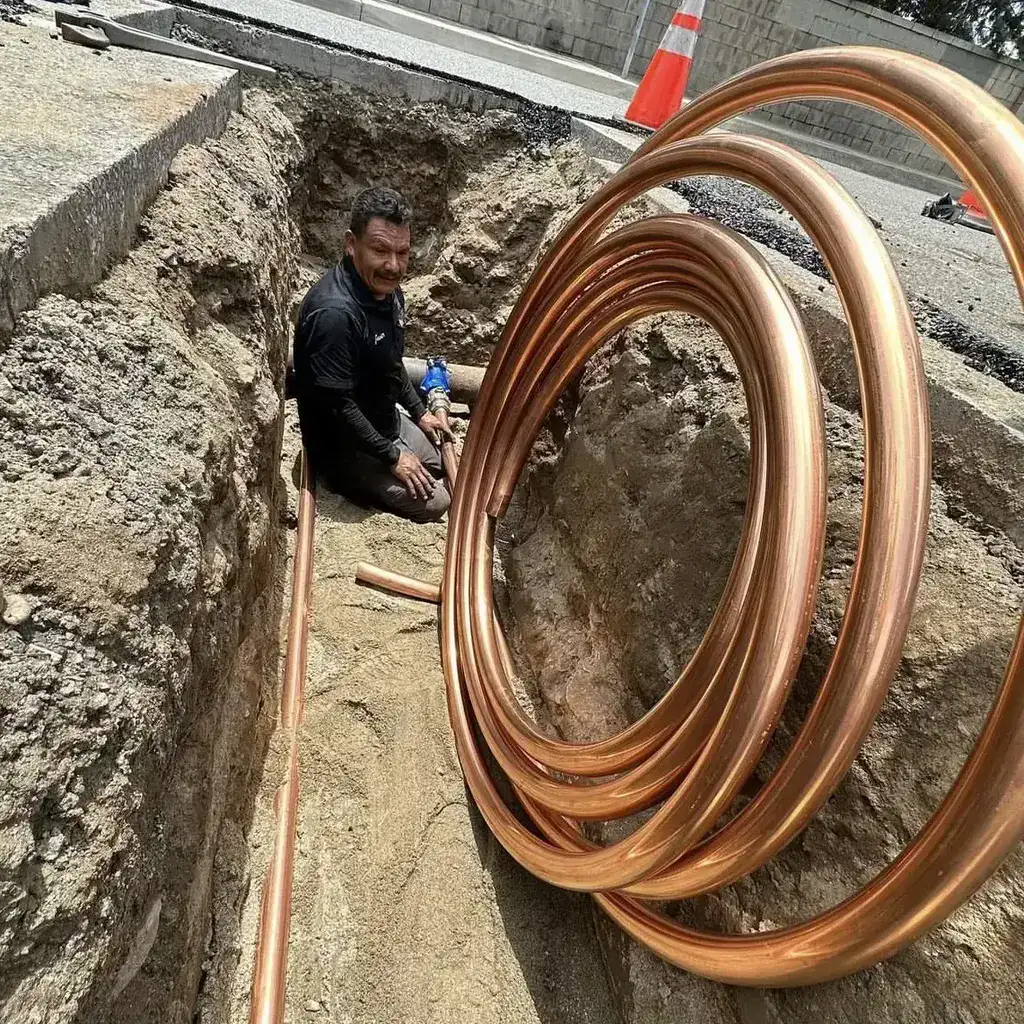
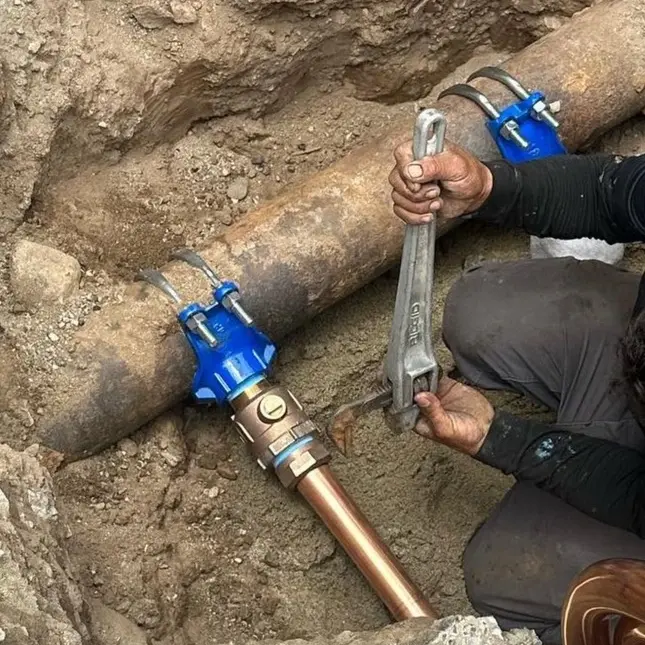
Applications of Hot Tapping Pipeline Services
Hot tapping pipeline services are used in a variety of situations, including:
- Pipeline Extensions: Adding new branches to an existing pipeline system to expand operations or connect to new infrastructure.
- Repairs and Maintenance: Performing maintenance or repairs on live pipelines without disrupting the flow of product.
- Emergency Situations: Quickly addressing issues in a pipeline, such as installing a bypass, without shutting down the system.
- Instrumentation: Installing monitoring devices, meters, or valves to track pipeline performance while the system remains online.
Benefits of Pipeline Hot Tapping
No Shutdown Required: The biggest advantage of hot tapping is that it allows for modifications or repairs to be made without shutting down the pipeline, reducing downtime and avoiding disruptions to operations.
Cost-Efficiency: By eliminating the need to stop and restart pipeline systems, hot tapping reduces costs associated with downtime, lost production, and restart procedures.
Minimized Environmental Impact: Since the flow of product continues during hot tapping, there is less risk of environmental contamination or hazardous material exposure, as the pipeline remains sealed throughout the process.
Versatility: Hot tapping can be performed on a wide range of pipeline systems, regardless of the material being transported, including water, oil, gas, and chemical products. It can be applied to pipelines made of various materials like steel, plastic, and cast iron.
Challenges and Considerations
Skill and Expertise: Hot tapping is a highly technical process that requires skilled professionals and specialized equipment. Improper handling can lead to serious safety risks, including leaks, explosions, or other accidents.
Equipment Costs: The specialized equipment required for hot tapping can be costly. This includes the hot tapping machine, cutting tools, and fittings necessary for safely performing the operation.
Pipeline Condition: Not all pipelines are suitable for hot tapping. If a pipeline is too old, damaged, or has weak points, hot tapping may not be feasible. A thorough inspection must be carried out before the procedure to ensure the pipeline can handle the operation.
Pressure and Flow: Hot tapping is typically safe for pipelines operating at moderate pressures. However, for pipelines carrying extremely high-pressure contents, alternative methods or additional safety measures may be required.
Safety Considerations
- Leak Prevention: The hot tapping process is carefully managed to ensure that no leaks occur during or after the procedure. Specialized sealing mechanisms are used to maintain the pipeline’s integrity.
- Fire and Explosion Risks: For pipelines carrying flammable materials, strict safety protocols must be followed to prevent accidental ignition. This may involve using non-sparking tools and ensuring the area around the pipeline is free from ignition sources.
- Personal Protective Equipment (PPE): Workers performing hot tapping must wear appropriate PPE, such as fire-resistant clothing, gloves, helmets, and eye protection to safeguard against potential hazards.
While hot tapping offers numerous advantages, including cost-efficiency and reduced downtime, it also requires a high level of expertise, careful planning, and specialized equipment to execute safely. Proper risk management and adherence to safety protocols are essential to ensure successful hot tapping procedures in live pipelines.
Hot tapping offers several key advantages, particularly in terms of maintaining continuous operation and reducing downtime, making it an invaluable technique in industries where pipeline shutdowns are costly or impractical. However, it also requires specialized skills, equipment, and careful risk management to avoid potential hazards. Weighing the pros and cons can help determine if hot tapping is the best option for a specific pipeline project or situation.
The Pros and Cons of Hot Tapping
Hot tapping is a specialized technique used in pipeline systems to create new branch connections or perform repairs without shutting down the flow of product within the pipeline. This process is widely used in industries such as oil, gas, water, and chemicals to minimize disruption and maintain continuous operation. While hot tapping offers several advantages, it also comes with certain drawbacks. Below are the key pros and cons of hot tapping:
Pros of Hot Tapping
-
Continuous Operation
The primary benefit of hot tapping is that it allows for pipeline modifications or repairs without shutting down the system. This is crucial for industries where interruptions in service can lead to financial losses, operational delays, or safety concerns. -
Cost-Effective
By eliminating the need to halt pipeline operations, hot tapping reduces downtime, which translates into significant cost savings. There’s no need for expensive shutdowns, restart procedures, or loss of production, making hot tapping a highly economical option for pipeline work. -
Minimized Environmental and Safety Risks
Since the pipeline remains sealed during the hot tapping process, the risk of leaks or spills is minimized. This is particularly important when dealing with hazardous or environmentally sensitive materials, as it reduces the potential for accidents or contamination. -
Flexibility and Versatility
Hot tapping can be applied to various types of pipelines, whether they carry gas, oil, water, or chemicals. It also works on different materials, including steel, cast iron, and plastic, making it a versatile solution for different applications and industries. -
Quick Response in Emergencies
In emergency situations, hot tapping allows operators to make quick repairs or install bypasses without shutting down the system, helping to avoid potentially dangerous situations or costly delays.
Cons of Hot Tapping
-
Specialized Skills and Equipment
Hot tapping requires a high level of expertise and specialized equipment to perform safely. The process involves drilling into a pressurized pipeline, and any mistake can lead to significant safety hazards, such as leaks, explosions, or injury. This makes it essential to have skilled professionals and the right tools on hand, which can increase the complexity and cost of the procedure. -
Potential for Pipeline Damage
While hot tapping can be performed on most pipelines, older or damaged pipes may not be suitable for this procedure. If the pipe material is compromised or if the pressure is too high, hot tapping could exacerbate the problem or cause further damage. -
Limited Pressure Range
Although hot tapping is generally safe for moderate-pressure pipelines, it may not be suitable for systems operating under extreme pressures or temperatures. Additional safety measures or alternative techniques may be needed in such cases, which could complicate the process and increase costs. -
Equipment and Setup Costs
The equipment used for hot tapping, including the hot tap machine, cutting tools, and specialized fittings, can be costly. While hot tapping saves money by preventing downtime, the initial investment in equipment and labor is still significant. -
Safety Risks
Even though hot tapping is generally a safe and controlled process, it still involves risks, particularly when working with high-pressure or flammable materials. Strict safety protocols must be followed, and any mishandling of the equipment can result in accidents or system failures.